The filter in the hydraulic system is an important part of keeping the system clean and running properly. However, due to various reasons, the filter may have oil leakage problems, which not only wastes energy and pollutes the environment, but also may lead to abnormal operation of the equipment, reduced efficiency, and even serious downtime losses. Therefore, it is essential to prevent oil leakage from the filter. Here's how to prevent leaks from the filter:
1. Install pipes correctly in the hydraulic system
(1) Avoid poor pipe bending: When assembling a hard pipe, the pipe should be bent according to the specified bending radius, otherwise it will produce different bending internal stresses and gradually produce leakage. Under normal circumstances, the radius of the bend of the hard pipe should be greater than 3 to 5 times the outer diameter of the pipe.
(2) Pay attention to the use of pipeline environment: During the working process of the hydraulic system, we should always pay attention to changes in the environment. If the hose is improperly installed, it is easily deformed by the influence of the environment, resulting in oil leakage accidents.
(3) Reasonable fixed installation: avoid forced assembly when installing tubing, which will deform the pipeline, produce installation stress, and easily hurt the pipeline, resulting in decreased strength; Pipe clamp fixed to be appropriate, too loose or too tight will strengthen friction and vibration, or the surface of the pipe clamping deformation, resulting in oil leakage.
2. Prevent high oil temperature in the hydraulic system
(1) Control in the work: correctly adjust some parameters of the hydraulic circuit, such as the output flow and pressure of the hydraulic pump should not exceed the specified value, and should be as low as possible under the normal working conditions of the system. Prevent close proximity to high-temperature objects during work. If the ambient temperature is high, insulation materials should be used to isolate the system from external heat sources.
(2) Daily maintenance: often make the oil level in the tank at the required height, keep the water in the cooler sufficient, the pipeline smooth, and give full play to the cooling effect. In addition, it is also necessary to choose the appropriate hydraulic oil.
3. Avoid oil contamination in the hydraulic system
(1) Strictly purify hydraulic oil: the hydraulic system should be configured with crude and fine filters as needed, the filter should be checked and cleaned frequently, and the damage should be replaced in time. Before filling oil into the oil tank, the oil tank and hydraulic pipeline must be thoroughly cleaned, and the filter screen should be placed at the filling port when filling hydraulic oil, and the filling should be in a place without wind and sand and pollution-free.
(2) Regular inspection and replacement of oil: the hydraulic oil should be checked regularly, and once it is found that the performance does not meet the requirements, it should be replaced in time. The hydraulic system should be changed after 1000 hours of cumulative work.
(3) Maintenance of hydraulic equipment and components: the construction machinery or hydraulic equipment parked in the open should be covered with a cloth, do a good job of dust prevention, rain and snow prevention, after rain and snow should be timely water removal, drying and rust prevention. For hydraulic components do not disassemble easily, if it is necessary to disassemble, the parts should be cleaned and placed in a clean place, and impurities should be prevented from falling into the components when reassembling.
4. Correct selection and assembly of seals
(1) Choose the right seals: Choose different types of seals according to the actual situation. For example, O-rings are suitable for stationary and rotating motion seals; Y-ring wear-resistant, suitable for reciprocating sealing. When receiving, check the factory time, deformation, aging and size.
(2) Correct assembly of seals: careful installation to avoid being splined, threaded and other sharp edge scratches, through the shaft keyway, threaded parts should use guiding tools, do not use metal tools assembly, to prevent scratching the seal ring and may make it twisted. Pay attention to the correctness of the direction, the directional seal lip installation not only fails but also may cause oil leakage.
5. Use of high-quality components
(1) Use high-quality seals and gaskets: Use high-quality seals and gaskets designed for specific hydraulic pump and system applications to prevent premature wear and oil leakage.
(2) Use the right type of hydraulic oil: Make sure to use the right type of hydraulic oil for the specific pump and system application, the wrong type of oil can cause seals and gaskets to age, which can lead to oil leakage.
6. System maintenance and monitoring
(1) Regular maintenance and inspection: Regularly check the hydraulic pump and system components for signs of wear or damage. Identify potential problems in a timely manner to prevent small problems from becoming big ones.
(2) Tighten bolts and joints: Use appropriate torque Settings to prevent leakage due to too tight or too loose.
(3) Hydraulic fluids with additives: Consider using hydraulic fluids with additives that regulate and protect seals and other components to reduce the risk of leakage and extend service life.
(4) Training of operators and maintenance personnel: Training on proper operation and maintenance procedures for hydraulic systems helps prevent damage to pumps and other components and reduces the risk of leakage.
7. Deal with leaks quickly
Timely solution of leakage problems: Once a leak is found, it should be resolved immediately to prevent further damage or contamination of the hydraulic system. Depending on the extent of the leak, hydraulic pump components may need to be replaced or repaired.
To sum up, the prevention of filter oil leakage needs to be started from a number of aspects, including correct installation of pipelines, preventing excessive oil temperature, avoiding oil contamination, correct selection and assembly of seals, the use of high-quality components, maintenance and monitoring, and quick handling of leakage problems. Each aspect has its importance and is interrelated to ensure the normal operation and reliability of the hydraulic system. Only by strictly implementing these measures can we minimize the risk of filter oil leakage and ensure the long-term stable operation of the equipment.
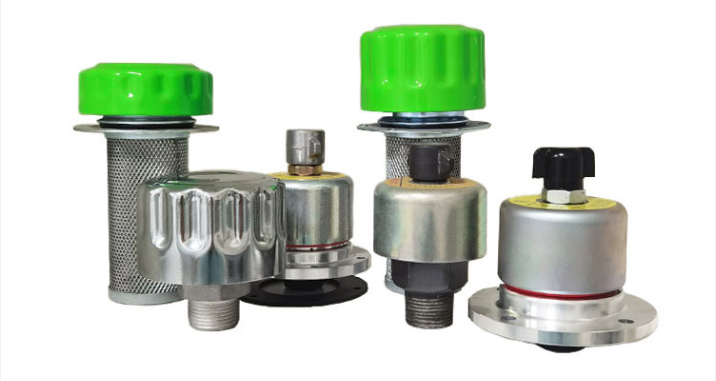